Оборудование и технология обработки материалов резанием
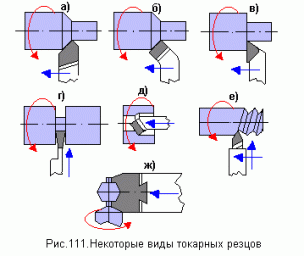
Физические основы процесса резания металлов и сплавов
Обработка металлов и сплавов и других конструкционных материалов резанием на металлорежущих станках - весьма распространенный производственный процесс, назначением которого является придание поверхностям заготовки с помощью режущего инструмента правильной геометрической формы, размеров и соответствующей чистоты поверхности. На большинстве машиностроительных заводов трудоемкость обработки резанием составляет до 60% от общей трудоемкости изготовления машин и поэтому совершенствование технологии резания металлов является актуальной задачей. Изучение закономерностей и явлений, связанных с резанием металлов, конструкцией режущих инструментов и металлорежущих станков, необходимо не только для управления процессами резания, но и для проектирования более совершенных технологических процессов изготовления деталей машин и приборов.
Процесс резания можно рассматривать как процесс местного сжатия и сдвига металла инструментом с последующим образованием стружки. Слой металла, подлежащий срезанию, находится в сложнонапряженном состоянии. Упруго-пластическим деформациям подвергаются не только срезаемые слои металла, но и близлежащие, расположенные впереди инструмента и под ним. На рабочие поверхности инструмента действуют значительные контактные напряжения, вызывающие износ инструмента. Процесс резания сопровождается значительным выделением тепла.
Стружка. В процессе резания различных материалов могут образовываться следующие основные виды стружек: сливные (непрерывные), скалывания (элементные) и надлома (рис.106).
Наклеп. В процессе резания пластическая деформация происходит не только в срезаемом слое, но и в поверхностном слое основной массы металла. Пластическое деформирование вызывает изменение физических свойств металла: повышает его твердость, снижает относительное удлинение и ударную вязкость, т.е. происходит упрочнение или наклеп металла. Степень упрочнения и глубина наклепанного слоя детали зависят также от начальных свойств обрабатываемого материала, геометрии и остроты режущего инструмента, режима резания, применения смазочно-охлаждающей жидкости. Пластичные металлы более склонны к упрочнению, чем менее пластичные. Увеличение подачи и глубины резания увеличивает наклеп. Увеличение скорости резания и применение смазочно-охлаждающих жидкостей способствуют уменьшению наклепа.
Нарост. При обработке пластичных металлов в определенном диапазоне режима резания на передней поверхности инструмента вблизи. режущего лезвия появляется так называемый нарост, который обладает высокой твердостью. Нарост-результат своеобразного явления схватывания-адгезии, имеющей место на участке контакта между стружкой и передней поверхностью инструмента под действием высоких температур и давлений. Нарост не удерживается постоянно на передней поверхности инструмента. Периодически, с большой частотой, он разрушается и срывается, ускоряя при этом износ режущей кромки инструмента, ухудшая чистоту обработанной поверхности, нарушая стабильность процесса резания. Применением смазывающе-охлаждающих жидкостей и тщательной доводкой режущих поверхностей инструмента вероятность появления нароста можно уменьшить.
Износ и стойкость инструмента. Износостойкость режущей части инструмента характеризуется его способностью сопротивляться микроскопическим разрушениям на поверхностях контакта. В общем случае износ инструмента является сложным процессом, состоящим из нескольких самостоятельных, каждый из которых может определять общую интенсивность износа. В зависимости от того, какой вид износа является преобладающим, следует предъявлять различные требования к свойствам материала инструмента. Различают следующие виды износа.
Абразивный износ-результат скалывания, срезания и смятия неровностей на контактных поверхностях режущего инструмента пои относительном движении. Этот вид износа преобладает при обработке хрупких материалов, а также материалов с твердыми составляющими структуры.
Адгезионный износ заключается в непрерывно происходящих процессах схватывания и последующего отрыва мельчайших частиц материала инструмента. При оптимальных режимах резания преобладает этот вид износа.
Диффузионный износ наблюдается при обработке сталей твердосплавными инструментами на высоких скоростях резания. Он наступает тогда, когда температура контактных поверхностей превышает критическое значение начала химического взаимодействия твердого сплава с обрабатываемым материалом.
Тепловые явления при резании, смазывающе-охлаждающие жидкости-СОЖ. При резании металлов почти вся механическая работа деформации и трения переходит в теплоту. Выделяющаяся при резании теплота существенно влияет на процесс резания и прежде всего на износ инструмента. Источником образования теплоты является работа, затрачиваемая на упруго-пластическую деформацию срезаемого слоя металла, и работа сил трения. Нагрев режущего инструмента и обрабатываемой заготовки в ряде случаев оказывает большое влияние на точность обработки, в частности на точность размеров обрабатываемых поверхностей и точность их геометрической формы; на износ инструмента. Применение СОЖ оказывает на процесс резания следующие действия: охлаждающее-отвод теплоты, смазывающее-снижение сил трения и износа инструмента, способствует удалению стружки из зоны резания и др. В качестве смазывающе-охлаждающих жидкостей применяются эмульсии и масла (растительные, животные, минеральные и др.).
Основные элементы процесса резания материалов
Заготовками для механических цехов являются прокат (круг, квадрат, полоса, трубы и др.), поковки, штамповки, отливки. Заготовки, поступающие в механические цехи, имеют припуск на обработку резанием. Припуск снимается различными способами обработки резанием. Виды обработки материалов резанием различаются между собой конструкцией используемого режущего инструмента и характером относительных движений, совершаемых инструментом и обрабатываемой заготовкой на металлорежущем станке.
Движения на металлорежущих станках. На металлорежущих станках существуют следующие движения: главное, подачи и вспомогательное. Главное движение определяет величину скорости резания. При токарной обработке (рис.107,а) главное движение обозначено цифрой 1 (вращение обрабатываемой детали), движение подачи - 2. При фрезеровании (рис.107,б) главное движение 1 определяется вращением фрезы; 2 - движение подачи. При строгании (рис.107,в) главным движением 1 является перемещение резца относительно детали или, наоборот, детали относительно резца, что физически равноценно; движение подачи 2 есть перемещение обрабатываемой детали на двойной ход резца в направлении, перпендикулярном к главному движению. Главное движение по величине, как правило, значительно больше движения подачи. Вспомогательными движениями являются установочные перемещения суппортов, задней бабки, поворот резцедержателя, перемещения траверсы и другие.
Геометрические параметры токарного резца. Токарный резец (рис.109) состоит из головки (рабочей части) и тела
К элементам рабочей части резца относятся передняя и задняя поверхности и режущие кромки. Передней поверхностью 1 называется поверхность резца, но которой сходит стружка. Задними поверхностями называются поверхности резца, обращенные к обрабатываемой детали. Различают главную 2 и вспомогательную 3 задние поверхности. Режущие кромки образуются пересечением передней и задних поверхностей резца. Различают главную 4 и вспомогательную 5 режущие кромки. Главная режущая кромка выполняет основную работу резания, и она, как правило, длиннее вспомогательной. Место сопряжения главной и вспомогательной режущих кромок называется вершиной резца. Вершина резца в плане может быть острой, закругленной или в виде прямой линии, называемой переходной кромкой.
Углы резца рассматриваются в главной 1 и вспомогательных секущих плоскостях 2 и в плане (рис.110). Главная секущая плоскость резца - плоскость, перпендикулярная к проекции главной режущей кромки на основную плоскость. В этой плоскости рассматриваются следующие углы:
Кроме перечисленных углов имеется еще один угол, характеризующий резец, это угол наклона главной режущей кромки λ -угол между главной режущей кромкой и линией, проведенной через вершину резца параллельно основной плоскости. Этот угол измеряется в плоскости, проходящей через главную режущую кромку перпендикулярно основной плоскости. Угол λ считается положительным, если вершина резца является низшей точкой режущей кромки; отрицательным - если вершина резца является высшей точкой режущей кромки; равным нулю, когда главная режущая кромка параллельна основной плоскости.
Углы режущей части резца влияют на процесс резания. Задние углы α и α1 уменьшают трение между задними поверхностями инструмента и поверхностью обрабатываемой заготовки, что ведет к снижению силы трения и уменьшению износа резца; однако чрезмерное увеличение заднего угла приводит к ослаблению режущей кромки резца. Рекомендуется при обработке стальных и чугунных деталей задние углы выполнять в пределах 6 ÷12º. С увеличением переднего угла γ уменьшается работа, затрачиваемая на процесс резания, и повышается класс чистоты обработанной поверхности. При обработке мягких сталей γ =8 ÷20º, а при обработке весьма твердых сталей - даже отрицательный угол γ = -5 ÷ -10º.
Главный угол в плане φ определяет соотношение между радиальной и осевой силами резания. При обработке деталей малой жесткости угол φ принимается близким или равным 90º , так как в этом случае радиальная сила, вызывающая изгиб детали, минимальна. В зависимости от условий работы принимается φ=10÷90º. Наиболее распространенной величиной угла резца в плане при обработке на универсальных токарных станках является φ = 45º. Вспомогательный угол в плане φ1 = 0 ÷ 45º; наиболее распространен φ1 = 12 ÷ 15º.
Угол наклона главной режущей кромки λ определяет направление схода стружки. При положительном λ стружка имеет направление на обработанную поверхность, при отрицательном - на обрабатываемую поверхность. Угол λ часто принимается равным 0º. Величины углов γ и α зависят от расположения резца относительно оси заготовки.
Кроме углов, определяемых при неподвижном (статическом) состоянии резца и заготовки, различают так называемые кинематические углы (или углы в движении) при вращении заготовки и подаче резца. Кинематические углы несколько отличаются от статических.
Токарные резцы. Материалы для изготовления режущих инструментов
Токарные резцы подразделяются по форме головки (правые и левые), изогнутости головки (вправо или влево, вверх или вниз), конструкции (цельные и составные), сечению стержня (прямоугольные, квадратные, круглые), по назначению: проходные, подрезные, отрезные, расточные, резьбовые, фасонные и др.
Проходные резцы применяются для наружной обточки; они могут быть черновыми и чистовыми, прямыми и отогнутыми (рис.111,а,б).
Материалы для изготовления режущих инструментов. Режущие кромки инструментов в процессе работы находятся под действием больших давлений и, кроме того, нагреваются до высоких температур, поэтому инструментальные материалы должны обладать:
1. Высокой твердостью и износостойкостью.
2. Высокой теплостойкостью - способностью сохранять режущие свойства при высоких температурах.
3. Высокой прочностью и ударной вязкостью.
4.Технологичностью и экономичностью - хорошей обрабатываемостью и минимальным содержанием дефицитных легирующих элементов без ущерба для режущих свойств.
Режущие инструменты целиком или частично изготовляются из инструментальных сталей и твердых сплавов.
Углеродистые инструментальные стали применяются для изготовления слесарно-монтажных и ручных режущих инструментов, работающих при малых скоростях резания. Зубила, отвертки, ножницы изготовляются из стали марок У7и У7А. Пробойники, ножи, пуансоны, керны, пилы, ножовки - из стали марок У8,У8А ÷ У10,У10А; слесарные метчики, напильники - из марок стали У11,У11А ÷ У13,У13А. В маркировке этих сталей буква Уобозначает, что сталь углеродистая, цифра указывает содержание в стали углерода в десятых долях процента, буква А - качественная (с меньшим содержанием серы и фосфора).
Низколегированные инструментальные стали (9ХС, ХВГ, Х и др.) применяются для изготовления инструментов, работающих при сравнительно небольших скоростях резания. Из стали марки Х изготовляются метчики, плашки; из стали 9ХС - сверла, развертки, фрезы, метчики, плашки; ХВГ применяется для изготовления протяжек, длинных метчиков и разверток.
Быстрорежущие стали. Эти стали имеют значительное содержание легирующих элементов, таких как вольфрам, ванадий, хром, молибден, кобальт. После соответствующей термической обработки они приобретают высокую твердость и имеют теплостойкость до 500-650ºС, что позволяет использовать их при увеличении скорости резания по сравнению с углеродистыми сталями в три-четыре раза.
Типичный представитель этих сталей - сталь Р9, Р18, весьма универсальные и технологичные. Высокие режущие свойства этих сталей обеспечиваются легированием их вольфрамом (~9% и ~18% вольфрама соответственно).
Группа быстрорежущих сталей повышенной производительности характеризуется введением в их состав ванадия, кобальта и молибдена. Добавление ванадия повышает износостойкость режущих инструментов за счет весьма твердых его карбидов. К этой группе сталей относятся также марки Р18Ф2, Р9Ф5, Р14Ф4. Недостатком ванадиевых сталей, ограничивающих их использование, является их низкая обрабатываемость шлифованием.
Добавление кобальта позволяет существенно повысить теплостойкость быстрорежущих сталей и их износостойкость. Это в свою очередь открывает возможность обработки жаропрочных и нержавеющих сталей. К этим сталям относятся марки Р18К5 (РК5), Р18К10 (РКЮ), Р9К5, P9K10. Однако эти стали более дорогие, чувствительны к ударным нагрузкам.
В последние годы все более широкое применение получают вольфрамомолибденовые инструментальные стали Р6М5, Р9М4 и др. Достоинством этих сталей является более равномерное распределение карбидов, что повышает их прочность и ударную вязкость.
Твердые сплавы делятся на металлокерамические и минерало-керамические и выпускаются в виде различных пластинок, применяемых для оснащения режущих кромок инструментов. Инструменты, оснащенные пластинками из твердых сплавов, допускают особенно высокие скорости резания, так как их теплостойкость значительно выше, чем у инструментов из быстрорежущих, а тем более углеродистых сталей. Кроме того, твердые сплавы обладают большой сопротивляемостью истиранию. Металлокерамические твердые сплавы разделяются на вольфрамовые (однокарбидные), вольфрамотитановые (двухкарбидные), вольфрамотитанотанталовые (трехкарбидныс). Вольфрамовые сплавы (группы ВК.) состоят из карбидов вольфрама WC и цементирующей связки-кобальта. Вольфрамотитановые сплавы (группа ТК) состоят из карбида вольфрама WC, карбида титана TiC и кобальта. Вольфрамотитанотанталовые сплавы {группы ТТК) состоят из карбидов вольфрама, титана, тантала и кобальта.
По марке твердого сплава можно судить о химическом составе става Буква К с последующей цифрой обозначает содержание кобальта в процентах. Так: в сплаве ВК6 имеется 6%, кобальта остальное (94%) - карбиды вольфрама. Содержание карбидов титана в сплаве группы ТК дано цифрой после буквы Т. Например, в сплаве Т5К10 имеется 5% карбидов титана, 10% кобальта, остальное (85%)-карбиды вольфрама. В группе вольфрамотитанотанталовых сплавов (ТТК) после второй буквы Т дается суммарное содержание карбидов титана и карбидов тантала в процентах. Так, в сплаве ТТ7К15 содержится 7% карбидов титана и тантала, 15% кобальта, остальное (78%) - карбиды вольфрама.
Сплавы группы ВК применяются при обработке деталей из чугуна. При обработке стальных деталей следует применять сплавы группы ТК и ТТК. Сплавы группы ТТК по прочности и стойкости занимают промежуточное положение между быстрорежущей сталью и твердым сплавом Т5К10. С увеличением содержания кобальта сплавы становятся менее хрупкими, их прочность при изгибе увеличивается. Поэтому сплавы с большим содержанием кобальта применяются при черновой обработке, с меньшим содержанием кобальта - при чистовой. Минералокерамические твердые сплавы - относительно новый инструментальный материал, имеющий благодаря его значительной дешевизне при высоких эксплуатационных свойствах. Минералокерамика представляет собой окись алюминия Аl2O3, подвергнутую специальной термической обработке и выпускаемой в форме пластинок белого цвета разнообразных профилей и размеров. Минералокерамика превосходит металлокерамические твердые сплавы по твердости и теплостойкости, но значительно уступает им в отношении вязкости и теплопроводности. Резцы с минералокерамическими пластинками применяются на чистовых операциях, т. е. при работе с высокими скоростями резания.
Режим резания и геометрия срезаемого слоя. На металлорежущем станке обычно совершается два рабочих движения: главное движение, которое определяет скорость деформирования металла и отделения стружки, а также движение подачи, которое обеспечивает непрерывность процесса резания. В случае токарной обработки главное движение - вращение заготовки, а движение подачи - поступательное перемещение резца (рис.112).
Скорость резания v - это скорость перемещения точки режущего лезвия инструмента относительно обрабатываемой поверхности заготовки в направлении главного движения. Она измеряется в метрах в минуту и определяется по формуле
v = (π·D·n)/1000,
где D - диаметр заготовки, мм (по обрабатываемой поверхности);
n - число оборотов заготовки в мин.
Глубина резания t (мм) - расстояние между обрабатываемой и обработанной поверхностями, измеренное в направлении, перпендикулярном к последней за один проход:
t = (D—d)/2 ,
где d -диаметр заготовки по обработанной поверхности, мм.
Величины S и t определяют номинальную площадь f, мм2, поперечного сечения срезаемого слоя металла
f = t ·S .
Объем металла, срезаемый за одну минуту: G = v·S·t, см3/мин.
Основное (технологическое) время обработки поверхности заготовки определяется из соотношения
То =( L·h)/(n·S·t),
где L - путь перемещения инструмента при обработке поверхности заготовки за один проход, мм;
h - припуск на сторону, мм. Отношение h/t = i - число проходов.
Толщиной срезаемого металла а называется расстояние между двумя последовательными положениями главного режущего лезвия инструмента за время одного полного оборота заготовки. Ширина срезаемого слоя b -расстояние между обрабатываемой и обработанной поверхностями, измеренное по поверхности резания. Согласно данным, приведенным на рис.112,
а =S·sinφ; b = t / sinφ;
f = St = a·b .
Приведенные соотношения показывают, что при неизменных t и S можно изменять форму поперечного сечения срезаемого слоя металла за счет изменения величины главного угла в плане.
2.9.4. Классификация металлорежущих станков
Металлорежущие станки делятся на группы в зависимости от вида технологических операций, выполняемых на них. Все станки разделены на девять групп: 1) токарные; 2) сверлильные и расточные; 3) шлифовальные, полировальные и доводочные; 4) комбинированные; 5) зубо- и резьбообрабатывающие; 6) фрезерные; 7) строгальные, долбежные и протяжные; 8) разрезные и 9) разные.
В обозначении модели станка первая цифра обозначает номер группы в той последовательности, как они перечислены. Так, токарные станки имеют в обозначении модели первую цифру 1, а фрезерные 6. Каждая группа станков разделена на девять типов, каждый из которых объединяет станки по их назначению, степени автоматизации, компоновке, например, вертикально-сверлильные, радиально-сверлильные, горизонтально-расточные.
Вторая цифра модели станка обозначает номер типа. Следующие две или одна цифра обозначают одну из технических характеристик станка.
Буква после первой цифры или в конце обозначения модели указывает на модернизацию или модификацию базовой модели станка. Так, например, станок 1К.62: цифра 1 - первая группа-токарный; буква К - станок модернизированный; цифра 6 - тип станка - токарно-винторезный; цифра 2 - станок с высотой центров 200 мм,.
Станок 2Н135А: цифра 2 - вторая группа (сверлильный станок); буква Н - станок модернизированный; цифра 1 - вертикально-сверлильный; цифры 35 - максимально допустимый диаметр сверления в мм в стали средней твердости; буква А - станок может работать в автоматическом режиме.
Станок 736: цифра 7 - седьмая группа (строгальные, долбежные и протяжные станки); цифра 3 - поперечно-строгальный (шепинг); цифра 6 - максимальный ход ползуна 600 мм. Приводом станка называется механизм, который передает движение от электродвигателя к исполнительным органам станка. Различают приводы главного движения, движения подачи и вспомогательных движений.
В металлорежущих станках главное движение передается от электродвигателя с помощью коробки скоростей, позволяющей изменять числа оборотов шпинделя или двойных ходов стола. Как правило, коробки скоростей обеспечивают ступенчатое регулирование чисел оборотов.
В некоторых случаях находят применение приводы бесступенчатого регулирования: фрикционные, электрические, гидравлические. Они позволяют установить любое заданное число оборотов шпинделя станка в определенных пределах.
Привод подачи, как правило, осуществляется от какого-либо звена главного движения, а иногда (фрезерные станки) от отдельного электродвигателя. Изменение величины и направления подачи осуществляются с помощью коробки подач, сменных зубчатых колес, реверсивных механизмов.
Обработка заготовок на токарных станках
Токарные станки получили наибольшее распространение, они