Технология обработки крупномодульных закаленных зубчатых колес твердосплавными червячными фрезами.
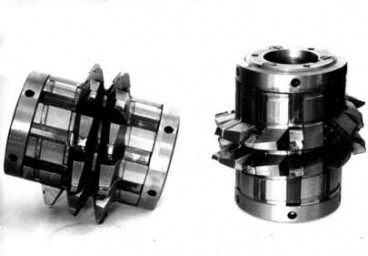
Разработанная еще в 80-х годах в отделе Новых Технологических Процесов НПО НИИПТМАШ технология удаления основного припуска закаленных крупномодульных зубчатых колес продолжает и сегодня совершенствоваться нашим предприятием, которое является правоприемником НПО НИИПТМАШ в области новых технологических процессов и инструмента.
Весьма сложным является процесс удаления основного припуска закаленных крупномодульных зубчатых колес под зубошлифование. Для решения задачи снятия основного припуска под зубошлифование, разработана технология формообразования и конструкция червячных твердосплавных фрез m=10мм с чередующимися коническими зубчатыми рейками . Данные фрезы используются для предварительной, под зубошлифование, лезвийной обработки закаленных венцов тепловозов характеристикой m=10; zk=65;
βd=oo; сталь 20Х2Н4А; HRC 50-55.
После химико-термической обработки зубчатые колеса подвергаются значительной деформации, что требует оставления припуска на зубья под последующее зубошлифование в пределах 0,7-1 мм.
Такой припуск существенно увеличивает машинное время зубошлифования, составляющее в среднем 4-6 часов. Кроме того, съем большого припуска абразивным кругом вызывает большие внутренние напряжения растяжения в поверхностном слое зубьев, что, в свою очередь,приводит к образованию микротрещин и других дефектов.
Обработка колес производилась на вертикально-зубофрезерных станках моделей 53Н11 и 5К32 встречным фрезерованием, без применения смазывающе-охлаждающей жидкости. Режимы резания следующие:
глубина резания t=0,3-0,5мм;
подача фрезы S=2мм/об;
частота вращения фрезы n=1,3-1,6 сек-1.
Рис.1
Универсальные однокорпусные фрезы m=10 мм с регулируемыми коническими зубчатыми рейками.
Машинное время обработки одного венца составляет 1,5 часа. Применение предварительной лезвийной обработки позволило снизить трудоемкость последующего зубошлифования венцов в 1,8 раза при высоком качестве обработанной поверхности зубьев.
Заточка фрез выполнялась в специальном устройстве к универсально-заточному станку (рис. 2), и на специальном заточном станке мод. В3-253Ф2.
Для приводных шестерен уникальной рудоразмольной мельницы мод. ММС 105-24 разработан технологический процесс зубофрезерования закаленных зубьев двухкорпусными универсальными твердосплавными фрезами m=28 мм, используемыми для предварительной обработки под зубошлифование со следующей характеристикой: m=28 мм; z=41; b=1030 мм; βd=6о25'; сталь 34ХН3МА; 50…55HRCэ.
Погрешность зубьев после закалки ТВЧ на длине 1030 мм составила 0,6–0,9 мм. Поэтому перед зубошлифованием производилась предварительная лезвийная обработка зубьев червячными твердосплавными фрезами.
Обработка производилась на вертикально-зубофрезерном станке мод. 5343 (рис. 3), встречным фрезерованием за один проход при следующих режимах резания:
t=0.4 мм;
S=2 мм/об;
V=0.3 м/сек.
Рис. 2.
Заточка твердосплавной фрезы на специальном устройстве к универсально-заточному станку.
Рис. 3.
Лезвийная обработка закаленной приводной шестерни мельницы ММС 105-54.
Машинное время обработки составило 40 часов. Износ зубьев фрезы по задним граням после указанного времени обработки составил 0,4-0,5 мм, что подтверждает достаточную для предварительной обработки стойкость инструмента.
Под зубошлифование был оставлен припуск 0,3 мм на сторону зуба.
Применение предварительной лезвийной обработки позволило в 4 раза сократить трудоемкость малопроизводительных зубошлифовальных операций.
Отработана технология чистовой обработки зубьев уникального зубчатого венца рудоразмольной мельницы ММС105-54 специальными твердосплавными фрезами (рис. 4) m=28 мм. Характеристика венца следующая: m=28 мм; zk=284; βd=6o25'; b=1000 мм; сталь 35ХМЛ; НВ 220-260.
Рис. 4
Специальная червячная двухкорпусная фреза двухстороннего резания αк=19о20′.
1 – корпуса фрезы;
2 – дистанционное кольцо.
Для зубчатых венцов диаметром ф8000мм разработана технология чистового зубофрезерования твердосплавнми червячными фрезами (рис. 5) на вертикально-зубофрезерном станке мод. КУ-306 с диаметром планшайбы ф8000 мм. Направление фрезерования используют встречное, режимы резания следующие: t=0,6 мм; S=3,86 мм/об; nф=20 об/мин.
Машинное время чистовой обработки венца составляет 65 часов.
Максимальный износ зубьев фрезы после указанного непрерывного времени работы не превысил 0,4 мм, что в 2-3 раза меньше, чем при аналогичной обработке быстрорежущими червячными фрезами.
О высокой стойкости фрезы свидетельствует и то, что разность толщин зубьев обработанного венца у верхнего и нижнего торцев не превышает 0,06 мм.
Применение твердосплавных фрез позволяет повысить производительность чистового зубофрезерования крупногабаритных венцов, по сравнению с быстрорежущими стандартными фрезами, в 1,5 раза при одновременном повышении точности изготовления по направлению зубьев.
Рис. 5. Чистовое зубофрезерование венца m=28 мм; zk=284; βd=6o25′; b=1000мм, на уникальном станке мод. КУ-306
Наиболее широкое применение различные конструкции твердосплавных фрез получили в производственных условиях крупнейшего машиностроительного завода Укрианы ЧАО «НКМЗ». Фрезы используют для предварительной, под зубошлифование лезвийной обработки закаленных колес m=16-36 мм; zk=12-86; b=200-700 мм; βd=0о-28о; Da=400-1800 мм; сталь 20ХН3А; HRC≥55; используемых в прокатных станах «2500»,«3600» и «5000».
Зубофрезерование осуществляется червячными твердосплавными фрезами (рис. 6).
Обработка колес ведется на тяжелых зубофрезерных станках мод. 5В375, 5353, ZFWZ – 3150/30 ABHVS «Modul» (ФРГ) без
применения смазывающе-охлаждающих жидкостей (рис. 7), (рис. 8).
Направление фрезерования используется встречное и попутное. Режимы резания при обработке закаленных зубьев следующие:
глубина резания: t=0,5 -0,8 мм за один проход;
подача фрезы: S=1.5-3 мм/об;
частота вращения фрезы: n=10-20 мин-1;
скорость резания: V=10-20 м/мин.
а) б)
Рис. 6.
Универсальные двухкорпусные фрезы одностороннего резания :
а) – со вставными зубчатыми рейками m=16 мм;
б) – со вставными зубьями m=20мм.
В течении 3-х лет было обработано свыше 250 закаленных зубчатых колес под последующие зубошлифование.
Применение фрез позволило устранить деформации зубьев после термообработки и снизить припуск под зубошлифование с 1-2,5 мм до 0,3-0,5 мм на сторону зуба.
Результаты промышленного внедрения технологии лезвийной обработки позволили установить следующее:
– имеющиеся на ЧАО «НКМЗ» зубофрезерные станки мод. 5353, 5В375 позволяют стабильно вести предварительную обработку закаленных колес твердосплавными червячными фрезами новой конструкции;
– разработанные конструкции червячных фрез технологичны и экономичны в изготовлении и эксплуатации;
– достигаемые качество и точность лезвийной обработки достаточны для обеспечения после зубошлифования 6-7-й степени точности колес по ГОСТ 1643-81;
–применение лезвийной обработки позволило за счет уменьшения припуска снизить трудоемкость малопроизводительных, но дорогостоящих операций зубошлифования на уникальных станках мод. ZSTZ-2500 и мод. HSS-460 фирмы «МааГ» (Швейцария) в 3-4 раза.
Разработаная технология чистовой лезвийной обработки крупногабаритных зубчатых венцов твердосплавными фрезами специальной конструкции (рис. 9). Обработка (рис. 10) производилась на вертикально-зубофрезерном станке мод. ННА-750А фирмы «Шибаура» (Япония), встречным фрезерованием с применением охлаждающей жидкости – масло индустриальное 20.
Рис. 7.
Лезвийная обработка закаленного шевронного зубчатого колеса в редукторном цехе ЧАО «НКМЗ»
m=28мм;
z=48;
β=27o26′;
b=390 мм;
сталь 20ХН3А,
HRC≥55
Чистовое нарезание венца
m=20 мм;
zk=268; β=5o15′;
b=700 мм;
сталь 35ЛIII,
НВ=140-160
осуществляется за один проход при режимах резания:
t=0,9мм;
S=4,72мм/об;
nфгр=30 об/мин;
Vрез=32м/мин.
Машинное время обработки одного венца составляет 24 часа, что в 1,8 раза меньше, чем при обработке быстрорежущей фрезой конструкции ЧАО «НКМЗ».
Рис. 8. Лезвийная обработка закаленной вал-шестерни в редукторном цехе ОАО «НКМЗ».
m=32 мм;
z=22;
β=28o21′;
b=575 мм;
сталь 20ХН3А,
HRC≥55
Максимальная потребляемая станком мощность составляет 7,6 кВт, что соответствует его загрузке на 26%.
Шероховатость отработанных поверхностей зубьев соответствует Ra=10мкм. максимальная разница в толщине обработанных зубьев между верхним и нижним торцем составляет 0,1 мм.
Заточка и переточка фрез осуществляется на специальном станке-полуавтомате с ЧПУ мод. В3-253Ф2.
Также разработана технология предварительной, под зубошлифование, обработки закаленных колес червячными фрезами, оснащенными неперетачиваемыми сменными поворотными твердосплавными пластинками.
Освоено изготовление универсальных фрез m=10-36 мм одностороннего и двухстороннего резания (Рис. 11), оснащенных пластинками из сплавов ВК10-ОМ, ВК10- ХОМ.
Рис. 9. Специальная червячная двухкорпусная фреза двухстороннего резания m=20 мм.
Фрезы одностороннего резания (рис. 11, а) состоят из двух корпусов:
левого и правого с конической винтовой нарезкой одного направления.
Каждый из корпусов фрезы, в свою очередь, выполнен из двух одновитковых частей для обеспечения удобства фрезерования гнезд под твердосплавные поворотные пластинки, расположенные исходя из условий тангенциального резания.
Обработка колеса такими фрезами осуществляется за два прохода:
вначале левым корпусом обрабатывают левые боковые поверхности зубьев колеса, а затем, после смены корпусов на зубофрезерной оправке, правым корпусом обрабатывают правые боковые поверхности зубьев или наоборот.
У однокорпусной фрезы двухстороннего резания (Рис. 11, б) так же, как и у фрезы одностороннего резания, корпус выполнен из двух одновитковых частей, скрепленных шпильками и гайками, но поворотные твердосплавные пластинки и крепежные винты размещены на обеих боковых поверхностях цилиндрических витков корпуса.
Рис. 10. Чистовое нарезание зубьев венца m=20 мм; zk=268; b=700 мм на станке мод. ННА-750А.
При этом, пластинки располагаются только вдоль линий станочного зацепления инструмента, или в 1÷3 ряда с перекрытием, продлевая, таким образом, боковую режущую кромку. На вершине витков также расположены твердосплавные пластинки, что позволяет производить такими фрезами предварительное формообразование зубьев.
Такая конструкция фрезы позволяет обрабатывать обе боковые поверхности зубьев колеса за один проход, т.е. в два раза производительней, чем фрезой одностороннего резания. Вместе с тем, фреза одностороннего резания более экономична по расходу твердосплавных пластинок, так как в диапазоне модулей m=10-36 мм для одного корпуса требуется только 29 пластинок.
Большим преимуществом разработанных фрез является то, что в диапазоне модулей m=10-65 мм они оснащаются одинаковыми по размерам твердосплавными пластинами, тоесть, сняв пластины с фрезы модуль m=10 мм можно оснастить ими фрезу m=65 мм. Это позволяет обработать колеса всего вышеуказанного диапазона модулей и существенно экономить твердый сплав.
а)
б)
Рис. 11. Червячные универсальные фрезы, оснащенные неперетачиваемыми поворотными пластинками:
а- правый корпус фрезы одностороннего резания m=20;
б- однокорпусная фреза двухстороннего резания m=20.
Расчет и проектирование червячных твердосплавных фрез осуществляется в CAD программах с получением твердотельной модели.
Производится разработка управляющей программы для обработки пазов под тангенциально расположенные пластинки на станке с ЧПУ.
Машинное время фрезерования пазов одного корпуса фрезы составляет Тмаш=16÷20 н.час.
Зубофрезерование закаленных колес на станках мод. 5В375 и ZFWZ-3150/30 фирмы «Модуль» (ФРГ) осуществляется без применения охлаждения, встречным или попутным фрезерованием, при следующих режимах резания: t=0.5…1.5 мм; S=1.5…2 мм/об; V=0.25 м/сек.
На станке мод. Р1200/1600 (рис. 12) фирмы «Gleason-Pfauter»(Германия) и при оснащении фрез твердым сплавом фирмы «Fette» (Германия) скорость резания увеличивается до V=0.65 м/сек.
Стойкость фрез новой конструкции до первого затупления в 1,8…2,0 раза выше, чем у напайных фрез, благодаря тангенциальному расположению пластин, отсутствию в них внутренних напряжений, а также благодаря нанесению на них износостойкого покрытия из нитрида титана.
Рис. 12.
Предварительная обработка закаленного колеса m=16 мм; z=41; β=0o;b=450 мм; сталь 20ХН3А, HRC≥55 на станке «Gleason-Pfauter» (ФРГ).
Применение предварительной лезвийной обработки зубьев закаленных колес разработанными твердосплавными фрезами позволяет снизить трудоемкость малопроизводительных зубошлифовальных операций в зависимости от модуля колес в 3-4 раза.
Твердосплавные червячные фрезы опробованы и внедрены и на других предприятиях, в частности, на таких предприятиях как ОАО «ЮУМЗ» (г. Орск), ОАО «Сибтяжмаш» и ОАО «Крастяжмаш» (г.Красноярск) и др.
Рекомендации по режимам резания твердосплавными червячными фрезами разработаны на основе проведенных лабораторных и производственных исследований с учетом оборудования, материала и твердости обрабатываемых колес, материала режущей части фрезы, и др.
Припуск на толщину зуба для чистого нарезания следует распределять эквидистантно эвольвентной поверхности зуба, а дно впадины обрабатывать в размер при черновом нарезании колес червячными, дисковыми или пальцевыми фрезами с «протуберанцем».
Глубина резания в зависимости от твердости заготовки и вида обработки приведена в табл. 1
Таблица 1
Глубина резания в зависимости от твердости заготовки и вида обработки
Глубина резания на один проход фрезы, мм | |||
Вид обработки | Твердость зубьев | ||
HB 260-320 | HRCэ35-50 | HRCэ>50 | |
Предварительная | 1,2 – 2,5 | 0,8-1,2 | 0,6-0,8 |
Чистовая | 0,8-1,2 | 0,5-0,7 | 0,3-0,5 |
Подача при работе фрезой назначается, исходя из твердости обрабатываемых зубьев и требуемой шероховатости. Величины подач приведены в табл. 2
Подача при чистовом нарезании зубьев
Таблица 2
Скорость резания при чистовом нарезании зубьев м/мин | ||||||
Тип станка | Модуль, мм | |||||
5-10 | 12-36 | |||||
HB≤320 | HRC≤45 | HRC>45 | HB≤320 | HRC≤45 | HRC>45 | |
Горизонтально- зубофрезерный | 30-25 | 25-20 | 18-20 | 15-20 | 12-15 | 10-12 |
Вертикально- зубофрезерный | 30-35 | 25-30 | 20-25 | 18-20 | 12-18 | 12-10 |
Указанная шероховатость поверхности зубьев обеспечивается при соблюдении следующих условий: работа на исправном станке соответствующей группы жесткости, жесткое закрепление заготовки,отсутствие вибраций в технологической системе СПИД, правильная заточка фрезы, равномерный припуск.
Скорость резания при чистовом нарезании зубьев назначается исходя из модуля обрабатываемых зубьев, типа зубофрезерного станка и твердости зубьев. Величина скорости резания приведена в табл. 3
Таблица 3
Скорость резания при чистовом нарезании зубьев
Скорость резания при чистовом нарезании зубьев м/мин | ||||||
Тип станка | Модуль, мм | |||||
5-10 | 12-36 | |||||
HB ≤32 0 | HRC≤4 5 | HRC>4 5 | HB≤32 0 | HRC≤4 5 | HRC>4 5 | |
Горизонтально- зубофрезерный | 30- 25 | 25-20 | 18-20 | 15-20 | 12-15 | 10-12 |
Вертикально- зубофрезерный | 30- 35 | 25-30 | 20-25 | 18-20 | 12-18 | 12-10 |
Примечание: скорости резания даны для случая жесткого крепления заготовки и резания без вибраций. При наличии вибраций скорость резания следует уменьшить.
Стойкость фрезы при обработке колес диаметром 8000-13000 с твердостью зубьев НВ 260-300 не менее 80 часов, а при твердости HRC>35 и диаметре 350-1500 мм – не менее 15 часов. Износ зубьев должен быть при этом не более 0,4-0,6 мм.
В табл. 4 приведен поправочный коэффициент Kv на скорость резания в зависимости от механических свойств режущей части инструмента.
Таблица 4
Поправочный коэффициент Kv на скорость резания в зависимости от механических свойств режущей части инструмента
Материал режущей части (твердый сплав) | Kv |
ВК10-ОМ | 1 |
ВК10-ХОМ | 1,1 |
импортный («Fette», ФРГ) | 1,5 |