Technology of processing coarse modular hardened gears with carbide-tipped worm cutters.
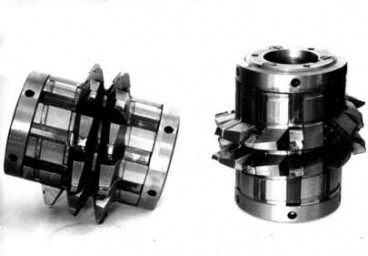
Developed as early as the 1980s in the Department of New Technological Processes, the NIIPTMASH technology for the removal of the main stock of hardened coarse-grained gears continues to be improved by our company today, which is the legal successor of the NIIPTMASH in the field of new technological processes and tools.
Processing for gear grinding is made by worm carbide cutters with bevel gears. The use of the technology of gear milling with carbide-tipped worm cutters allows to increase the productivity of the final milling of large-size coronets with diameter up to 12000 mm, in comparison with standard cutters made of high-speed steel, by 1.5 times with simultaneous increase in the accuracy of manufacturing gears
Very difficult is the process of removing the main allowance of hardened coarse-grained gears for gear grinding. To solve the problem of removing the basic allowance for gear grinding, the technology of shaping and the design of worm carbide cutters m = 10mm with alternating bevel gears has been developed. These cutters are used for preliminary, under gear grinding, for the processing of hardened locomotives of diesel locomotives with the characteristic m = 10; zk = 65;
βd = oo; steel 20Х2Н4А; HRC 50-55.
After chemical-thermal treatment, the gear wheels undergo considerable deformation, which requires leaving the allowance on the teeth for subsequent grinding in the range of 0.7-1 mm.
Such an allowance significantly increases the machine-assisted tooth grinding time, which averages 4-6 hours. In addition, the removal of a large allowance by an abrasive wheel causes large internal tensile stresses in the surface layer of the teeth, which in turn leads to the formation of microcracks and other defects.
The wheels were machined on vertical hobbing machines of models 53H11 and 5K32 with counter milling, without the use of a lubricating-cooling liquid. The cutting modes are as follows:
depth of cutting t = 0,3-0,5mm;
feed of the cutter S = 2mm / rev;
milling cutter speed