Rolling cylindrical surfaces
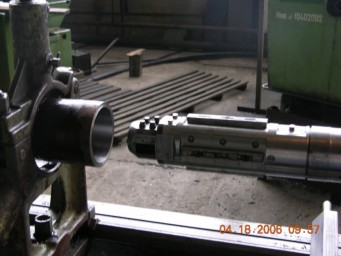
Rolling cylindrical holes is a method of finishing processing based on cold, thin plastic deformation of the surface layer of the metal of the workpiece. At the same time, the treated surface is strengthened (the main distinguishing feature of rolling) and the surface roughness decreases. Rolling holes is done on turning, drilling, horizontal boring and special machines with ball or roller plates. The hole for rolling is processed by boring or deployment. The processing allowance is 0.04 and 0.1 mm., The peripheral speed is 40 ... 250 m / min, the feed is 0.2 ... 0.5 mm. Rolling holes on radial drilling machines is performed when installing rolling in the spindle, and the detail on the table of the machine. On turning and revolving machines, the part rotates with the spindle, and rolling makes reciprocating movements. With the greatest technical and economic effect, rolling is used when machining large-diameter holes in heavy body parts, the abrasive treatment of which is difficult. The diameter of the hole after rolling increases by 0.02-0.03 mm, the hardness of the surface layer increases by 20 ... 50%, and therefore the wear resistance increases by 1.5-2 times. Rolling can be applied to holes of any diameter and length, both through and deaf. Rolling can be done without the use of coolant, and with the use of industrial oil or sulfofresol. When rolling with rollers, the most favorable results were obtained when the allowances for diameter were 0.03-0.06 mm, and when rolling with a ball, to 0.2 mm.