Problems with gear milling and methods of their elimination
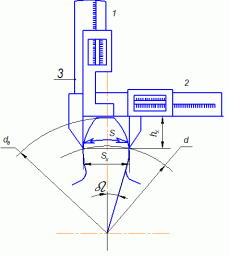
Рис. 140. Погрешности и элементы зубчатого колеса:
а — профиля зуба,
б — накопленная погрешность шага,
в —радиальное биение зубчатого венца,
г — отклонение шага,
6 — направления зуба,
е — пятно контакта,
ж — гарантированный боковой зазор,
з — измерительное межосевое расстояние
Отклонение от нормальной работы станка, а также любые неточности в установке детали, инструмента, гитар и др. в конечном счете отражаются на качестве нарезаемого зубчатого колеса. Контроль зубчатого венца осуществляется в соответствии с требованиями ГОСТ 1643—72. На рис. 140 приведены некоторые погрешности зубчатого колеса и их обозначения по ГОСТу, которые могут встретиться в практической деятельности наладчика. Часть неполадок можно устранить в процессе подготовки станка к работе, а некоторые — в процессе его подналадки. Ниже рассмотрены неполадки, наиболее часто встречающиеся в практике и устраняемые наладчиком.
1. Нельзя пустить станок в наладочном или автоматическом режимах
Возможные причины: неправильная регулировка реле давления, выключение тепловых реле электродвигателей и включение аварийных конечных выключателей.
Для устранения этих неисправностей необходимо в первую очередь проверить давление в гидросистеме станка (должно быть 18...20 кгс/см2). При падении давления до 14 кгс/см2 реле давления отключает станок.
Затем нужно проверить состояние тепловых реле в электрошкафу станка. При перегреве электродвигателей толкатель его теплового реле будет выдвинут до появления красной метки. После возврата толкателя в рабочее утопленное положение необходимо разобраться в причинах, приведших к перегреву электродвигателя. Такими причинами могут быть завышенные режимы обработки или заедание какого-нибудь рабочего органа станка. Если после проверки давления и тепловых реле станок не запускается, то следует проверить, не включены ли аварийные конечные выключатели хода суппорта. Для устранения этой причины упор, включающий конечник, отодвигают от него и включают обратный ход. Затем аварийный упор возвращают в прежнее рабочее положение.
2. Движение фрезерного суппорта во время осевой передвижки фрезы происходит рывками
Причиной этому может быть потеря давления в системе гидравлического зажима суппорта, в результате чего суппорт во время передвижки фрезы не отжимается и электродвигателю приходится преодолевать силы трения зажатого суппорта. Подобное явление, но в меньшей мере, может происходить при отсутствии смазки в направляющих суппорта. Для устранения этой неполадки в работе станка необходимо обеспечить гидравлический отжим суппорта поднятием давления в системе до требуемого уровня, а также наладить поступление смазки на направляющие.
3. При нарезании прямозубого колеса зуб не параллелен оси заготовки
Такое явление может быть при неточной настройке гитары деления, когда сменные зубчатые колеса, близкие по числам зубьев, установлены не на свои места. Причиной непараллельности зуба оси колеса также может быть незакрепление ведомого вала гитары дифференциала винтом, находящимся в опоре гитары. При этом под воздействием момента сил вращающихся колес дифференциала его корпус доворачивает заготовку в какую-нибудь одну сторону. Кроме указанных причин, такое же действие на заготовку оказывает ненадежное ее закрепление, особенно при использовании гидрозажима. Для устранения неполадки необходимо завернуть до упора винт, стопорящий ведомый вал гитары дифференциала, проверить настройку гитары деления и увеличить зажим заготовки.
4. При нарезании косозубого колеса происходит срезание зубьев
Срезание происходит, когда доворот заготовки от дифференциала для образования требуемого угла наклона зуба происходит в сторону, противоположную той, на которую повернут суппорт с фрезой. Для устранения этой неполадки необходимо проверить правильность настройки сменных зубчатых колес гитары дифференциала с учетом направления витков фрезы и направления нарезаемого зуба. Если фреза по отношению заготовки установлена правильно, то в сменные колеса гитары дифференциала нужно установить паразитное колесо для изменения направления доворота заготовки. Правильность настройки гитары можно проверить по эскизам, находящимся в руководстве по эксплуатации станка.
5. Большая погрешность нарезаемых колес по разности окружных шагов зубьев
Причины этой погрешности могут заключаться в погрешности кинематической цепи деления, неточной установке червячной фрезы, радиальном и торцовом биении заготовки и опорных поверхностей установочного приспособления, а также в биении центров стола и контр поддержки при нарезании колеса с установкой оправки в центрах. Устранение этих неполадок сводится к следующему. Проверяется зацепление сменных колес гитары деления. Ошибку окружного шага может вызвать как полное отсутствие зазора между зубьями сменных колес, так и слишком большой зазор. Проверка производится покачиванием колеса рукой. После этого проверяются посадочные места приспособления для крепления заготовки, а также базовые поверхности самой заготовки с замером их биений. Фактические величины биений не должны превышать допускаемых для данной степени точности нарезаемых зубчатых колес. Если на опорных торцах обнаружены забоины, то их нужно устранить шабровкой и зачистить оселком. При обнаружении радиального и торцового биения фрезы необходимо проверить состояние прилегаемых поверхностей и снова собрать оправку с фрезой. При необходимости можно установить фрезу более высокого класса точности.
6. Большая накопленная погрешность окружных шагов нарезаемых колес
К этой погрешности приводят те же причины, которые влияют на погрешность окружного шага, т. е. неправильное положение заготовки в установочном приспособлении, неправильное зацепление сменных зубчатых колес гитары деления, биение червячной фрезы, биение центров стола и котрподдержки. При исправлении этой погрешности особое внимание необходимо обратить на правильность установки заготовки. Надо устранить зазор между оправкой и посадочным отверстием заготовки, устранить биение оправки и самой заготовки, устранить отжим детали ведущим хомутиком при работе в центрах. При контроле точности нарезаемого колеса устанавливать его на прибор следует на ту же поверхность, на которой обрабатывались зубья.
7. Большая погрешность профиля зуба
Вероятными причинами появления погрешности профиля зуба является плохое качество фрезы (отклонение угла профиля зубьев, неточность шага витка, отклонение хода винтовых канавок, нерадиальность передней поверхности зубьев, неточность посадочного отверстия и торцов и т. д.), недостаточность нарезанной части фрезы, радиальное биение фрезы, биение заготовки, прогиб и отжим крепежного приспособления, погрешности делительной цепи станка, проявляющиеся несколько раз за время обкатки одного зуба. Для устранения причин, связанных с погрешностью инструмента, целесообразно заменить червячную фрезу, предварительно проверив ее точностные параметры. При установке фрезы на оправку следует тщательно выставить ее по радиальному и торцовому биению и надежно закрепить в шпинделе. Затем следует проверить, надежно ли закреплено установочное приспособление на планшайбе стола и не происходит ли заклинивания сменных зубчатых колес гитары деления.
8. Отклонение направления зубьев симметричное по обеим сторонам, так называемая конусность зубьев
Основной причиной этой погрешности является непараллельность движения фрезерного суппорта относительно оси вращения колеса в продольной плоскости станка. Такой характер отклонения направления зуба может быть и при интенсивном износе режущих кромок фрезы за время нарезания одного колеса. Непараллельность движения суппорта устраняется при отладке станка на соответствие геометрическим нормам точности. При интенсивном износе режущих кромок фрезы необходимо работать с уменьшенными режимами резания, исключающими появление вибраций н чрезмерного нагрева заготовки и фрезы.
9. Дробленая поверхность и следы вибрации на нарезаемых зубьях
Причиной дробления могут быть большие зазоры в заднем подшипнике, поддерживающем оправку с фрезой, и в переднем подшипнике шпинделя, большое расстояние между опорами оправки при малом ее диаметре, недостаточно жесткое крепление заготовки, малое число зубьев фрезы, отсутствие смазки в суппорте или столе. Для устранения указанных причин необходимо зазоры в подшипниковых опорах шпинделя и оправки всегда поддерживать на требуемом уровне, для чего периодически подтягивать гайкой передний подшипник скольжения у шпинделя, а при недопустимом износе втулки, поддерживающей опоры заменить ее. При появлении на поверхности зубьев дробления необходимо установить заготовку на более жесткое приспособление (с приближением опорном поверхности к нарезаемому венцу), а поддерживающий подшипник фрезерной оправки приблизить к шпинделю, удалив для этого с оправки промежуточные кольца. Для чистовой обработки фрезу следует выбирать с возможно большим числом зубьев.
10. Большая шероховатость поверхности зубьев колеса
Причины погрешности заключаются в плохой заточке фрезы, большом биении фрезы, нежесткости крепления фрезы и заготовки, загрязнении и неправильном выборе СОЖ большой продольной подаче. Для уменьшения шероховатости обрабатываемой поверхности необходимо сменить затупленную фрезу. Если эта мера не окажет своего действия, то нужно устранить нежесткость крепления фрезы и заготовки (как было описано выше) и сменить загрязненную СОЖ. Последней мерой является уменьшение величины продольной подачи, хотя это и снижает производительность обработки.